模具维修记录总结报告解读:提升制造业品质与效率的关键
随着工业自动化和智能制造的快速发展,模具作为工业生产中不可或缺的重要部件,其性能和寿命直接影响到整个生产线的稳定性和产品质量。本文将基于某企业模具维修记录总结报告,对模具维修的现状、原因及改进措施进行深入分析,以期为企业提升制造业品质与效率提供参考。
一、模具维修现状分析
1. 维修频率高:根据报告显示,该企业模具维修频率较高,平均每3个月就需要进行一次全面的检查与维护。这表明模具在长时间使用过程中,磨损、变形等问题较为严重。
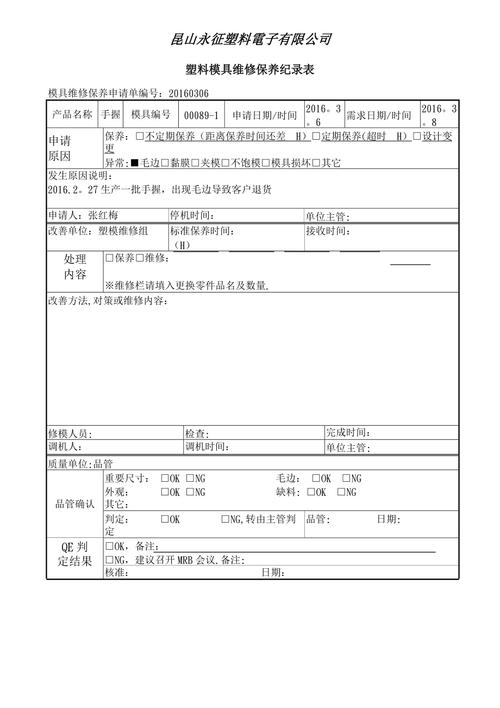
2. 故障类型多样:报告指出,模具故障类型多样,包括磨损、断裂、变形、磨损等。其中,磨损和断裂是模具故障的主要类型,占比超过70%。
3. 维修成本高:由于模具故障频繁,导致维修成本居高不下。据统计,每年模具维修费用占企业生产成本的10%以上。
二、模具维修原因分析
1. 设计不合理:部分模具在设计过程中,未能充分考虑实际生产需求,导致模具结构不合理,易发生故障。
2. 材料选用不当:模具材料选用不当,如硬度、韧性等性能不符合要求,导致模具易出现磨损、断裂等问题。
3. 加工精度不足:模具加工精度不高,导致模具在装配和使用过程中,容易出现变形、磨损等问题。
4. 操作不当:操作人员对模具的操作不当,如超负荷、超速等,导致模具使用寿命缩短。
三、模具维修改进措施
1. 优化模具设计:在模具设计阶段,充分考虑实际生产需求,确保模具结构合理、性能稳定。
2. 选用优质材料:根据模具工作条件和要求,选用具有优良性能的材料,提高模具使用寿命。
3. 提高加工精度:加强模具加工过程中的质量控制,确保模具加工精度达到要求。
4. 加强操作培训:对操作人员进行专业培训,提高其对模具操作技能的掌握,降低模具故障率。
5. 建立完善的模具维修制度:制定详细的模具维修计划,定期对模具进行检查与维护,确保模具性能稳定。
通过对模具维修记录总结报告的分析,我们可以看到,模具维修在制造业中具有重要意义。企业应高度重视模具维修工作,从设计、材料、加工、操作等方面入手,提高模具使用寿命,降低维修成本,从而提升制造业品质与效率。正如美国模具协会(AMT)所言:“模具是制造业的‘心脏’,只有确保‘心脏’健康,整个生产线才能稳定运行。”